hogyan végezzünk Idővizsgálatot a növény padlóján
egy dolog közös a modern fegyveres erők, a sportolók, a HR osztályok és A Szilícium – völgy tech cégei között-mindannyian Frederick Winslow Taylor által inspirált taktikákat és stratégiákat használnak, amelyeket gyakran a “tudományos menedzsment atyjának”neveznek.
Taylor ötletei, mint például a munkamorál javítása, a hulladék csökkentése és a termelési szabványok javítása, továbbra is hitelesek. Az egyik ilyen ötlet, amely kritikus fontosságú a növénypadló hatékonyságának javítása szempontjából, idővizsgálat formájában érkezik.
az idő-és mozgástanulmányok elvégzése nem szokványos feladat. Gondos előkészítést igényel egy jól átgondolt tervvel. Ebben a bejegyzésben felvázoljuk a folyamatot, és megmutatjuk, hogy mire kell vigyáznia, ha az első próbálkozásra rendbe akarja hozni a dolgokat.
mi az idővizsgálat?
a British Standards Institutions (BSI) az első számú testület, amelynek feladata a mérnöki és ipari termelési szabványok létrehozása az Egyesült Királyságban. A BSI így határozza meg az idővizsgálatot:
“az emberi munka megfigyelése, rögzítése és értékelése annak megállapítása érdekében, hogy egy képzett munkavállaló milyen időket igényel meghatározott munka elvégzéséhez meghatározott körülmények között, meghatározott munkaszakaszon.”
a “munka”, amelyre utal, magában foglal minden olyan tevékenységet a gyárban, amely hozzájárul a gyártási folyamathoz – kézi munka vagy gépek használata, gépkezelők, akik menet közben hoznak döntéseket stb.
az Idővizsgálatok a legalkalmasabbak olyan tevékenységekre, amelyek kiszámítható és ismétlődő cselekvéseket tartalmaznak. Ideálisak gyári beállításokban, ahol a gyártási folyamat szekvenciális feladatokra és kezelői mozgásokra bontható.
ilyen összefüggésben megméri azt az időt, amelyet egy adott feladathoz több munkavállaló végez, hogy megtalálja a szokásos időt (a számítást később a cikkben mutatjuk be). Az ipari tervezésben és gyártásban a standard idő az az átlagos idő, amelyet egy megfelelően képzett munkavállaló vesz igénybe egy meghatározott feladat elvégzéséhez.
az idővizsgálat olyan munkamérési tevékenység, amelyet általában képzett megfigyelő végez, olyan alapvető berendezések segítségével, mint a stopper és a vágólap az időfelvételek feljegyzésére. A modern gyárakban a megfigyelők fejlettebb eszközöket, például videokamerákat, számítógépeket, sőt speciális szoftvereket is használhatnak.
miért végezzen időelemzést?
ha megfelelő tervezéssel és gondos elemzéssel megfelelően végzik, az idővizsgálat részletes képet nyújt arról, hogy mennyire hatékonyan végzik a munkát az üzem padlóján. A standard idő felbecsülhetetlen mutató a vezetők számára, akik általában a termelési hatékonyság és a termelékenység javításának módjait keresik.
arra is használható, hogy rejtett hibákat és gyengeségeket találjon az üzem padlójának más aspektusaiban, például a gépek és munkaállomások optimálistól eltérő elrendezésében és elhelyezésében. A standard idő használatával megállapíthatja a munkaerő, a gépek és egyéb termelési inputok elosztásának hatékonyságát.
a költség-és hatékonyságnövelés mellett az időmérés is létfontosságú lehet a munkavállalók jóléte szempontjából. Segíthet a jobb, biztonságosabb munkaterületek létrehozásában. A vezetők azonosíthatják és eltávolíthatják a felesleges és potenciálisan veszélyes mozgásokat és akciókat az üzem padlóján, ezáltal csökkentve az egyes feladatok elvégzéséhez szükséges erőfeszítéseket.
rengeteg más előnye van az idővizsgálat elvégzésének:
- szükséges a termelési ütemtervek reális tervezéséhez
- segít az optimális munkaerő-elosztásban az üzem padlóján
- használható az alternatív folyamatokkal való összehasonlításhoz
- szükséges a munkavállalók közötti kiegyensúlyozott munkaelosztáshoz
- segít a célidők és a bérösztönzők létrehozásában
- segít kiküszöbölni a nem hatékony vagy felesleges műveleteket, és minimalizálja a munkavállalók erőfeszítéseit
- ha végzett karbantartó dolgozók, ez segíthet a karbantartási tervezők és vezetők, hogy jobban megtervezni és megszervezni a rutin karbantartási munka
a Standard idő nagyon hasznos mutató az ipari mérnökök és a gyártásvezetők számára. Lehetővé teszi számukra, hogy összehasonlítsák üzemük hatékonyságát az ipari szabványokkal. A mutató a jövőbeli tervezés szempontjából is értékes, a következő kulcsfontosságú szempontok becslésében:
- szállítási idők a jövő termék tételek
- jövő munkaerő követelmények és a munkaerő-költségek
- jövő gépek/termelési berendezések beruházási követelmények
- jövő nyersanyag beszerzési igények
- készletgazdálkodás
- teljes termelési költség és eladási ár egységenként
rengeteg oka van az idővizsgálatok elvégzésének. Lássuk, mi legyen a helyén, mielőtt elindítja a stopperórát.
a sikeres idővizsgálatok elvégzésének alapvető követelményei
az érintett iparágtól vagy termelési folyamatoktól függetlenül az idővizsgálatnak ugyanazok az alapvető követelményei lesznek.
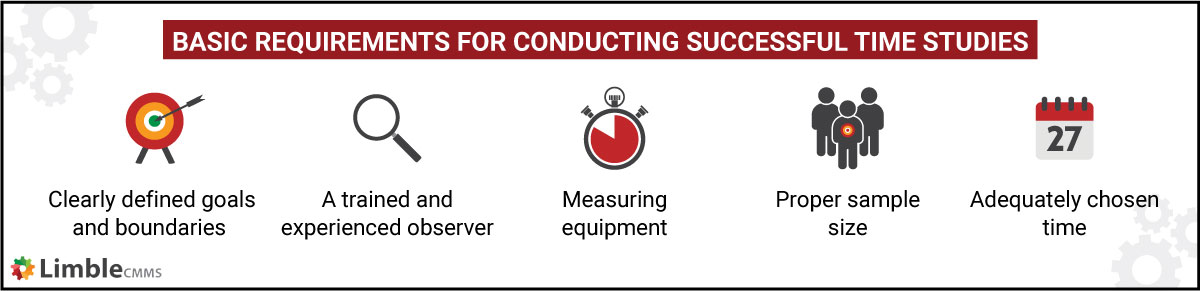
a következő 5 területre sorolhatjuk őket, amelyekkel foglalkoznia kell az időtanulmány elkészítésekor:
1) világosan meghatározott célok és határok
mielőtt elvégezné az idő-és mozgástanulmányát, egyértelmű határokat kell megállapítania.
először határozza meg és határozza meg a tanulmány céljait – a gyártási folyamat felgyorsítása, a pazarló tevékenységek eltávolítása stb.
Ezután válassza ki azokat a folyamatokat, amelyek a tanulmány középpontjában állnak. Nézze meg, hogy a szektor már létrehozta-e a szokásos időket, amelyeket referenciapontként használhat az összehasonlításhoz.
2) képzett és tapasztalt megfigyelő
ez az a személy, aki elvégzi az idővizsgálatot. A legtöbb esetben a megfelelő tapasztalattal és képzéssel rendelkező ipari mérnököket részesítik előnyben erre a munkára.
ideális esetben a munkahelyi optimalizálás tanúsításával kell rendelkezniük. A megfigyelőnek biztonságos és kényelmes kilátóponttal kell rendelkeznie, ahonnan megfigyelheti a munkavállalókat, miközben rendszeres feladatokat látnak el.
vannak olyan vállalatok, mint például az Industrial Time Study Institute, amelyek tanácsadási és képzési szolgáltatásokat kínálnak. Segíthetnek az idő tanulmányainak végrehajtásában és a technikai kérdések megválaszolásában.
3) felszerelésválasztás (alap vs haladó)
az időmérő berendezések szerepe drámai módon megváltozott az elmúlt években. A múltban a tanulmányokat egyszerű stopperórával és idővizsgáló táblákkal végezték, a megfigyelő közel állt a munkavállalókhoz.
ennek volt néhány jelentős hátránya, amelyek közül a legfontosabb a “Hawthorne – effektus” volt-a munkavállalók a szokásosnál több erőfeszítést tehetnek, ha tudják, hogy figyelik őket.
a modern technológia lehetővé teszi a megfigyelők számára, hogy távolról és titokban figyeljék és rögzítsék az időket, videoeszközök (CCTV) és speciális szoftverplatformok segítségével, amelyek helyettesíthetik a stopperórát és az alapidőtanulási felvételi táblákat.
4) megfelelő mintaméret
kellő gondossággal kell eljárni a munkaerő-minta méretének kiválasztásakor. Ha ez nem megfelelően nagy és reprezentatív a meglévő munkaerő, a munka mérése lesz gyakorlatilag haszontalan.
a munkavállalók minősége és kompetenciája szintén kritikus. Gyakori hiba a legjobban teljesítő egyének kiválasztása. Ehelyett válasszon egy kiegyensúlyozott mintaméretet, amely a jól képzett munkavállalóknak kedvez, de akiknek a munkája nem teszi őket alacsony vagy magas termelékenység szélsőségébe.
5) megfelelően kiválasztott idő
a hibahatár csökkentése érdekében az idővizsgálat általában több gyártási ciklus mérését foglalja magában. A gyártóüzemekben rövidebb határidőkkel és intenzívebb aktivitással rendelkező termelési időszakok lesznek az üzem padlóján.
ügyelni kell arra, hogy olyan időszakot válasszon, amely a létesítmény általános munkafolyamatát reprezentálja, kiszámítható határokon belül. Hacsak nincs konkrét célja, kerülje el azokat a csúcsidőszakokat, amikor idővizsgálatokat végez.
a folyamat felvázolása: hogyan kell idővizsgálatot végezni?
az idővizsgálatot lineárisan végzik, több világosan meghatározott lépéssel. A képesített megfigyelő a tanulmány megkezdése után a következő lépéseket teszi:
- válassza ki a tanulni kívánt feladatokat: ez a tanulmány céljaitól és a cég által meghatározott alapvető határoktól függ. Ebben meghatározó szerepet kap a gyártási tevékenység típusa és a termelési rendszerek jelenlegi állapota.
- elemezze az egyes feladatokat: a gyártás az iparágban már kialakult folyamatokat és szabványokat használja? Ha igen, a megfigyelő kiválaszthatja az alapszabványokat, és kalibrálhatja a mérési folyamatot, hogy azok tükrözzék azokat. Ha nincsenek standardok, a megfigyelőnek a saját tapasztalatát és ítélőképességét kell felhasználnia a legjobb alapvonal ábrázolásához.
- válassza ki a jogosult munkavállalókat: a megfelelően képzett átlagos munkavállalók reprezentatív mintájának kell lennie.
- becsülje meg a megfigyelendő ciklusok számát: több adatminta kevesebb hibahatárt eredményez, de több időt és erőfeszítést igényel. Itt idő-és költségvetési korlátok alapján egyensúlyozásra van szükség.
- közölje a tanulmány részleteit a munkavállalókkal: az idővizsgálatok zavaró hatással lehetnek a munkaerőre. Az emberek aggódni fognak a tanulmány jövőbeli munkahelyi biztonságára gyakorolt lehetséges következményei miatt. Nagyon fontos, hogy előzetesen közöljük a tanulmány célját.
- figyelje meg és rögzítse a dolgozó teljesítményét és idejét az egyes elemekhez: számos technika áll a megfigyelők rendelkezésére. Ha alapvető időórát használ, az időzítési módszerek közé tartozik a folyamatos módszer, a snapback módszer és a halmozott módszer. A fejlettebb eszközök és szoftverek lehetővé teszik a mérések automatizálását.
- használja a megfigyelt adatokat a standard idő kiszámításához: a képletet és a számításokat részletesen ismertetjük a következő szakaszban.
végül a számítások és a tanulmány kezdeti céljai alapján a vállalatnak képesnek kell lennie arra, hogy néhány cselekvhető következtetésre jusson.
a standard idő kiszámítása
miután a megfigyelő rögzítette a mintacsoport összes dolgozójának tényleges időértékeit, ideje kiszámítani a standard időt. A folyamat ezt a sorrendet követi:
- számítsa ki az átlagos időt
- számítsa ki a normál időt az átlagos idő és a minősítési tényezők használatával
- számítsa ki a normál időt a normál idő és a kibocsátási egységek használatával
Számítsa ki az átlagos időt
ahogy a neve is jelzi, ez az az idő, amelyet a munkavállaló a feladat elvégzéséhez az elejétől a végéig igénybe vesz. Ha több munkavállalót figyelnek meg a vizsgálat részeként, a megfigyelt idő átlagos értékét az összes rögzített időérték átlagának kiszámításával állítják elő, bármilyen rendellenes érték eltávolítása után.
határozza meg a minősítési tényezőket
a munkavállaló tényleges rögzített teljesítménye nem mindig felel meg a feladat “normál” szabványainak. A megfigyelőnek módosítania kell a megfigyelt időt, hogy levezethesse azt az időt, amelyet egy átlagos operátor a feladat elvégzéséhez igénybe vett volna.
ítélőképessége és tapasztalata alapján a megfigyelő meghatározhatja az egyes munkavállalók teljesítményértékelését. Az erre a célra használt népszerű minősítési rendszerek a következők:
- Pace/Speed Rating
- Westinghouse System
- objektív értékelés
- szintetikus Értékelés
ezek a minősítési rendszerek olyan tényezőket használnak, mint a sebesség, a készség, az erőfeszítés és a dolgozó következetessége teljesítményük értékeléséhez. A minősítési tényező százalékos értékként kerül kiszámításra, például 90% vagy 120%. Ez a várt teljesítménytől való eltéréseket mutatja, amely 100% – ban jelenik meg.
normál idő kiszámítása
ha az átlagos időt megszorozzuk a minősítési tényezővel decimális formátumban, akkor a tevékenység “normál idő” értékét kapjuk. Itt van a képlet:
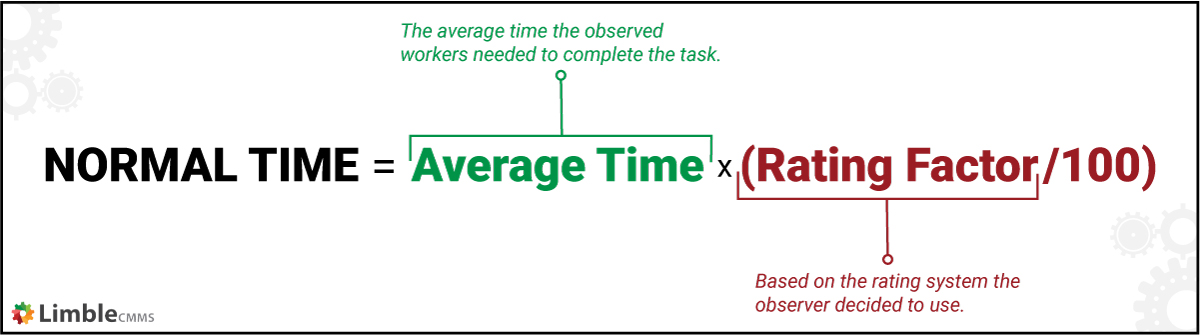
a normál idő eléréséhez a normál időt további “kibocsátási egységeknek” nevezett értékekkel kell beállítani.”
juttatások biztosítása
a valós munkakörülmények hatalmas hatással lehetnek az üzem padlóján dolgozó munkavállalók termelékenységére. Ezek a feltételek drasztikusan változnak az egyik termelési létesítményről a másikra. A megfigyelőknek figyelembe kell venniük ezeket a különbségeket.
számos tényezővel rendelkeznek, amelyek 5 fő kategóriába sorolhatók:
- relaxációs támogatás: magában foglalja a személyes szükségleteket (étkezés, víz, fürdőszobai szünetek stb.) és a fáradtság (magában foglalja az állandó időtartamot, a megvilágítás szintjét, a levegő minőségét, az erő alkalmazását, a fizikai és mentális megterhelést stb.).
- interferencia-támogatás: Ha a munkavállalónak több gépet vagy szerszámot kell üzemeltetnie, akkor ezt a juttatást arra használják, hogy figyelembe vegyék a gép állásidejét, amikor a munkavállaló más gépeken van elfoglalva.
- folyamat támogatás: ez a folyamat részeként vagy áramkimaradás, a gépek hibái stb.
- készenléti támogatás: Ez figyelembe veszi az összes szabálytalan és kiszámíthatatlan szünetet vagy késést (például a sürgősségi karbantartást), amely a gyártási folyamat során felmerülhet.
- különleges juttatás: bizonyos rutin tevékenységeket – például a berendezések indítását, tisztítását, leállítását és cseréjét-a vezetés ösztönzi a berendezések biztonságának és élettartamának javítása érdekében. Az e szünetek által okozott zavarokat figyelembe veszik e juttatás felhasználásakor.
a kibocsátási egységeket százalékok formájában adják meg, így felhasználhatók a standard idő végső kiszámításához.
Számítsa ki a szokásos időt
végül eljutunk a kulcsfontosságú mutatóhoz, amely megadja nekünk azt az időt, amelyet egy normál munkavállaló egy adott feladathoz igénybe vesz, amikor azt átlagos/szokásos körülmények között hajtják végre, figyelembe véve a jogos és elkerülhetetlen zavarok különféle juttatásait.
a normál idő eléréséhez meg kell szorozni a normál időt egy kibocsátási egység minősítési tényezővel. A képlet így megy:
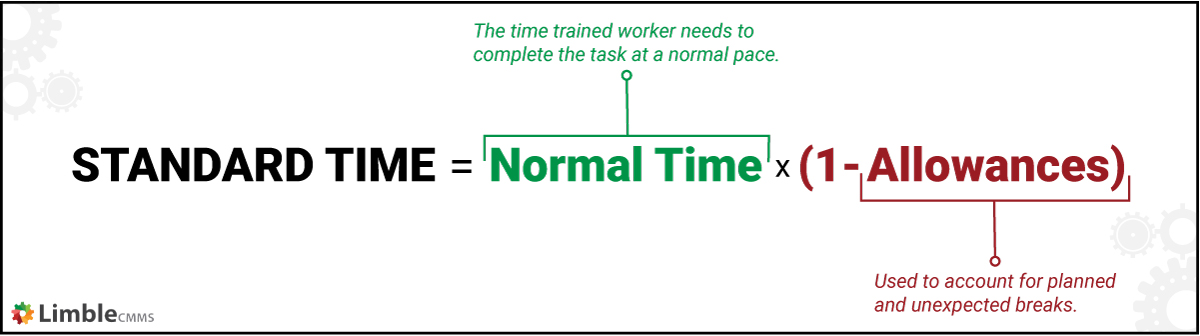
most mutassuk meg, hogyan működik ez egy tényleges példában.
gyártási idő vizsgálati példa
Vegyünk egy alapvető gyártási beállítást, ahol a munkavállalók egy vadonatúj létesítményben gyártanak hátlapokat autó fékbetétekhez. Képzelje el, hogy ezek a munkavállalók átlagosan 33 percet vesznek igénybe egy hátlapra.
a vállalat idővizsgálatot kíván végezni, hogy megtudja, hogyan viszonyul a gyár padlójának hatékonysága az ipari átlaghoz, és ha lehetséges, meghatározza azokat a területeket, amelyeken javítani lehet.
ennek a példának a kedvéért tegyük fel, hogy az egy tétel Hátlap előállításának várható időértéke 30 perc.
a mérések azt mutatják, hogy a munkavállalók körülbelül 10% – kal lassabbak a várt normánál. Tehát a megfigyelő biztonságosan hozzárendelhet egy 90% – os teljesítményértékelési tényezőt az egyszerű sebességértékelési módszerrel.
a munkaciklusok során megfigyelt különböző szünetek figyelembevétele érdekében a megfigyelő 7% – os relaxációs, 5% – os interferencia -, és egy másik 8% – os speciális juttatást ad hozzá, összesen 20% – ra.
tehát a következő ismert változókkal rendelkezünk:
- átlagos idő = 33 perc
- sebesség Értékelés = 90%
- kibocsátási egységek = 20%
a normál idő kiszámításához először ki kell számolnunk a normál időt az átlagos megfigyelt idő és sebesség alapján:
normál idő = átlagos idő X (sebességérték/100)
normál idő = 33 x (90/100)
normál idő = 29,7 perc
ezt 30 percre kerekíthetjük le – ez az az alapsebesség, amellyel a munkavállalóknak szünet vagy megszakítás nélkül kell végezniük a hátlap-tétel gyártását.
ezután kombináljuk ezt a normál időt a kibocsátási egységekkel, hogy megérkezzünk a szabványos időhöz, amikor egy tétel hátlapot gyártunk a gyárban:
normál idő = normál idő (1 – kibocsátási egység)
normál idő = 30 ÷ (1 – 20/100)
normál idő = 37,5 perc
amint a fenti számításokból láthatjuk, a létesítményben dolgozó munkavállalók által a hátlapok tételének előállításához szükséges szokásos idő, figyelembe véve a különböző tényezőket, például a sebesség besorolását és a szünet-juttatásokat, körülbelül 37 és fél perc.
az idővizsgálat számos olyan területet mutat be, ahol van mit javítani. Például a megfigyelt idő 33 perce azt mutatja, hogy a munkavállalók átlagosan nem teljesítenek az optimális szinten. Előfordulhat, hogy a vezetésnek meg kell határoznia a hatékonyság hiányának okait, és korrekciós intézkedéseket kell alkalmaznia.
a kibocsátási egységek egy másik terület, ahol a létesítmény javíthat. A relaxációs juttatás csökkentése negatív hatásokkal járhat – csökkent munkavállalói morál, megfelelőségi jogsértések (munkavállalói jogok) stb. Azonban, interferencia juttatás és különleges juttatás esetleg csípett, hogy tovább javítsa a termelékenységet.
a berendezés meghibásodása az egyik leggyakoribb oka a megszakításoknak a gyártási padlón. A legjobb módja annak, hogy harcba velük, hogy egy modern CMMS rendszert, hogy dolgozzon ki egy proaktív karbantartás menedzsment kultúra.
a siker kulcsa a folyamatos fejlesztés
ha el akarja távolítani a hulladékot a gyártási padlóról, akkor olyan fogalmakat kell elfogadnia, mint a sovány karbantartás és a folyamatos fejlesztés.
a hatékonyság javításának első lépése a teljesítménymutatókra vonatkozó konkrét adatpontok megszerzése. A gépekkel könnyű megjósolni a teljesítményt. De az őket működtető emberek sokkal kevésbé kiszámíthatóak.
egy idővizsgálat segít kitölteni ezt a kritikus űrt a gyártók számára. Az advent a modern technológia, ez most könnyebb, mint valaha, hogy végezzen pontos idő és mozgás tanulmányok. Mégis, ha a régimódi módon csinálod, csak egy stopperóra, egy vágólapra és egy kis türelemre van szükséged!